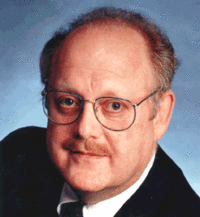
LEED consultants are paid to lend their expertise to achieve a project’s LEED certification goals. Their decisions focus on achieving credits and their participation is absolutely vital to the project, but some can actually work against the project's sustainability goals. Here are the top six problems I see.
#1 Discouraging bidding by specifying unrealistic LEED requirements
When a specification requires a regional source, a recycled content percentage, and certain certifications for a product, the specifier has to be certain that conforming products exist. On a recent project, the only bidder for the doors couldn’t actually meet all the requirements and put in a premium price. Other bidders declined to bid citing the requirements of the specifications. The worst outcome was a project that decided to abandon certification because of unnecessary requirements in the specifications that pushed the project over budget.
Solution: Don’t use the specifications as a research tool. Either find out what’s available and specify what you want the contractor to purchase, or give the contractor options and flexibility to meet the LEED requirements, using a mix of products.
#2 Not recognizing that performance is a sustainable attribute
There is a roofing product that has 100 percent recycled content, is 100 percent recyclable, and is made from 100 percent regional materials. Unfortunately, it is only guaranteed until the first rain, since it’s made out of papier-mâché.
Solution: Performance is more important than recycled content for roofing. Always seek the highest-performing roofing material with a 20-year track record (which includes PVC). If you’re not going to keep PVC out of the inside of your building, why be concerned about PVC on the roof? Personally, I doubt that either PVC, TPO, EPDM, or modified bitumen are edible, and am more concerned about the damage that water intrusion can have on the inside of a building when the roofing fails.
#3: Adding ‘their’ language to the specifications.
Sorry, poetic language doesn’t buy products, nor does repeating all the VOC levels in every spec section make sense. The specifications are contract documents that contain the qualitative requirements for materials and assemblies. Subcontractors must put in bids with only a few hours to evaluate a project.
Solution: Specify products that comply with LEED requirements and require the submittals necessary to document the required credits.
#4: Believing manufacturer’s product literature
Not too long ago a flooring manufacturer overstated its sourcing and FSC claims. The product as promised was not the product as delivered—they never had a source for FSC wood. …And then there was that article in the magazine that claimed brick would earn 26 LEED points. …And then there was that insulation manufacturer that was fined $155,000. by the FTC for false R-value claims.
Solution: Ask the manufacturer to submit a sample of LEED documentation from a previous project as an example, instead of relying on marketing literature.
#5: Issuing a LEED Scorecard with “maybe” as an option
We all recognize that achieving some credits is uncertain until construction is well underway. However, “maybe” means “no” to a subcontractor if extra expense is involved.
Solution: At least one LEED consultant will not include a scorecard in the project manual. Others will reissue the scorecard monthly. The important thing is to hold the contractor accountable for making sure that the overall target is achieved, with a little cushion to allow for missing or faulty documentation.
#6: Calling LEED “good enough”
LEED is intended to point the project in the right direction and open up conversations about sustainability goals, but too often its goals are adopted without critical review.
Solution: The consultant should engage with the client about their intentions and priorities, and then revisit those throughout. That gives them the tools to answer questions like: Do you abandon the requirement for FSC wood once you achieve 50%? Is it the scorecard or sustainability that governs?
Mark Kalin is President of Kalin Associates Specifications and currently Chair of CSI’s National Technical Committee. The firm has completed specs for over 200 LEED projects. Free spec downloads and position papers at www.kalinassociates.com.
Add new comment
To post a comment, you need to register for a LEEDuser Basic membership (free) or login to your existing profile.