EAp3: Fundamental Refrigerant Management calls for elimination of CFC-based refrigerants, to prevent ozone depletion. However, that’s just one piece of the environmental puzzle when it comes to refrigerants. Many CFC substitutes act as very strong greenhouse gases, contributing to global warming—and adding that piece of the puzzle is the focus of this credit.
EAc5 encourages significant reduction or elimination of all refrigerants in base building systems, and at the very least, works to promote use of refrigerants that have the lowest global warming potential.
Do you use CFCs?
If your building is still using CFC-based refrigerants, it will be very difficult to earn this credit. Likewise, this credit will be difficult if you are using inefficient base building equipment or if the majority of cooling is satisfied with multiple smaller systems, such as window units.
You’ll be in the best position to earn the credit with efficient, centralized chiller equipment using refrigerants with low ozone depletion and global warming potential.
It’s an accounting credit
This credit is basically an accounting credit to document the refrigerants used in your base building systems, determine the efficiency and leakage rates of your equipment and calculate the overall environmental impact of those refrigerants in terms of ozone depletion and global warming potential. Performing the required calculations will give you your “Total Refrigerant Impact Per Ton” value. That value must be less than or equal to 100 in order to achieve this credit.
Well-managed buildings should be tracking most of this information already and will simply need to plug all of the data into the provided calculator to determine credit compliance.
A lot of the required data for this credit can be found on a product data tag affixed to the equipment.
Start with a systems review
Start by verifying that your building fire suppression systems do not use halons, CFCs or HCFCs. If you find any of these chemicals, you won’t be able to earn the credit without converting those systems. Alternatives to these materials include HFCs, water, foam, and carbon dioxide.
If your building uses natural ventilation with no mechanical cooling, you can earn this credit without further analysis.
If your building uses mechanical or mixed-mode ventilation, collect information on all base building systems that use refrigerants, including manufacturer, model number, installation date, refrigerant type, and amount used in the equipment.
Retrofits unlikely
After performing the initial review, if a project finds that it doesn’t qualify for the credit, it’s rare for it to undergo an HVAC retrofit to earn the credit, due to the costs involved. However, the criteria can be a good set of guidelines for future HVAC projects.
Test and maintain your equipment regularly to minimize refrigerant leakage.
- Ideal refrigerants strike a good balance between efficient operation, minimal ozone depletion potential, and minimal global warming potential.
- The best HVAC equipment is efficient, has low leakage rates, and has a long service life.
- Implementation of a refrigerant management program will help you to track and minimize refrigerant leakage over the life of the equipment.
Building engineer must sign off
The required calculations may be performed internally using the provided calculator in the LEED Online credit form, but a building engineer must review the data and sign off in the designated space on the credit form. You may incur costs based on whether you have in-house personnel qualified to verify the refrigerant calculations or need to use a third party.
Consider these questions when approaching this credit:
- Do you keep records of all refrigerants used in base building systems? Does any of your HVAC equipment or fire suppression systems use CFCs, HCFCs or halons?
- How efficiently does your base building equipment use refrigerants? Do you have a refrigerant management program in place to minimize leakage?
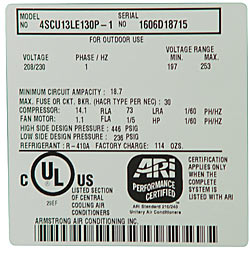
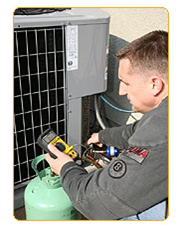