Background
This credit requires projects to perform a potable water analysis and then create a water treatment program for any cooling towers or evaporative condensers that will be installed.
The term “evaporative condensers” applies to closed circuit water cooling towers, closed circuit cooling towers that evaporate water to cool refrigerant, and rooftop HVAC units that incorporate evaporative condensing for the internal DX refrigerant cooling cycle.
The purpose of the testing is to make the treatment program appropriate for the specific water quality at the site and to minimize water usage while still protecting the equipment. Evaporation is an effective means of rejecting heat from the building to the atmosphere. Given the water availability challenges that many locations have, it is important to maximize the use of water; filtration and chemical treatment allow projects to get the most of the water used for cooling.
In any of the above noted units, warm water evaporates in the tower to remove the heat from the circulating water stream and is discharged to the atmosphere, thereby leaving the rest of the water in the tower sump or in the refrigerant heat exchanger sump. As that pure water vapor leaves the tower, any dissolved solids that might have been entrained, or chemicals that were mixed into the water, remain and build up in the water that is left behind in the tower.
“Solids” could refer to dissolved minerals that were already in the potable make-up water, or it could mean any other detritus blown into the tower, including rust, dirt, dust, plant seeds, leaves, or bird feathers. Tower systems must periodically blow-down (i.e. discharge to sanitary sewer) any water that has become too contaminated to recirculate. In addition to the evaporation, this blow-down requires fresh new potable water for make-up, both of which then require additional chemicals for treatment.
Normal HVAC system water treatment usually consists of:
-
Biocides: to kill any biological agents like algae or bacteria (including legionella, which is naturally occurring in water). At least two different biocides (“dual biocide”) are used in order to control all bacteria that may be present in the circulating water.
-
Corrosion inhibitors: to protect the unit and the sump, as most are made of steel (wet- ted surfaces can be specified to be made of stainless steel, which adds cost but also adds to useful equipment life).
-
pH adjustment: depending on whether make-up water is acidic or alkaline.
The chemical treatment needed and the costs associated with treatment will depend on the water quality at the site (the reason for the initial test), the volume of circulating water, and the system capacity/connected load. The ongoing cycle of adding make-up water, adding chemicals, and blowing down water to clean the system means that a chemical treatment approach will use the most water of the approaches described herein, but
it is needed in order to maintain the equipment in operating condition and get all the useful life potential out of the equipment. Poor chemical treatment almost guarantees extraordinary cleaning measures will be needed (at best) or, at worst, premature equipment failure.
Types of water filters
Using a sediment filter and an appropriate chemical treatment program can increase the number of times water can be recirculated in the tower system—the “cycles of concentration”— before being discharged to waste. This LEED credit looks to maximize the number of cycles of concentration, which therefore reduces water usage. Filters can take the form of direct or indirect media filters, or electronic filters.
- Sand filters, which are similar to swimming pool filters, directly filter water through sand, usually requiring a skimmer to be installed on the cooling tower to skim material off the surface of the tower sump. The sand will need periodic replacement.
- Metal filters, where the filter elements are generally permanent, and need periodic back-flushing to remove accumulated materials based on the differential pressure across the filter. Back-flushing uses additional water, and can occur anywhere from every 3–4 hours to every 3–4 days, depending on the amount of water moving through the filter and the amount of solids filtered out. Metal filters can be full-flow or partial-flow (also called side-stream) depending on the project budget and space available.
- Centrifugal solids separators use the force of circulating water spinning inside the filter to indirectly force particulates out of the circulating water, to be collected at the bottom of the filters where they can be discharged to drain. Solids separators can also be full- flow or partial-flow (also called side-stream) depending on the project budget and space available.
Most projects use some combination of filtration and chemical treatment to achieve the desired water quality.
Another option is an electrostatic filter, an example of which is the Clearwater Dolphin system. This unit creates an electric field through which condenser water passes as part of the pipe. The field is reported to kill organisms in the water while also imparting a charge to solid particles in the circulating water. The charged particles are attracted to each other to form larger particles which then precipitate out of the circulating water once velocity is reduced.
Such units are reported to greatly increase the number of cycles of concentration while almost eliminating the need for chemical treatment (an annual treatment of biocide may still be needed to fully control biological growth). A filter/separator should be used in conjunction with the electrostatic filter, or the particles can be collected in the tower sump.
Condenser water systems that run continuously all year long, such as water source heat pump systems, are the best application for these units. Since the unit relies on the circulating water moving the particles through the unit to treat the water, they are not suitable for condenser water systems that shut down for long periods of time, such as a seasonal water cooled water chiller. A separator/filter approach with standard chemical treatment may be a better choice for these systems.

WEp2: Indoor Water Use Reduction requires metering of cooling tower/evaporative cooler make-up water. Along with this, we would recommend a meter be installed on the overflow/blow-down/drain connection.
Generally, make-up water is metered in order to know how much water has been added over a certain period to ensure that appropriate chemical treatment is also added, and also to allow for a reduction in sewer charges for the evaporated water.
Having a meter on the discharge can help property managers understand water use better, and can also help projects negotiate municipal water and sewer discounts. Projects electing not to meter make-up water will have difficulty maintaining appropriate chemical treatment levels.

A typical 100,000 SF office building might have a nominal 300 ton cooling system, using either chilled water with an open cooling tower, water cooled AC units with an open cooling tower, or two rooftop HVAC units of 150 tons capacity. A single electrostatic filter on the open cooling tower would require an 8” pipe, but each of the two rooftop units would have 6” Dolphin units installed on the internal water circulation piping.

Price ranges for filters and separators depend on accessories and options chosen, especially shell and filter materials.
Cost Synergies
WEp2/WEc2: Indoor Water Use Reduction
WEp3/WEc4: Building Level Water Metering / Water Metering

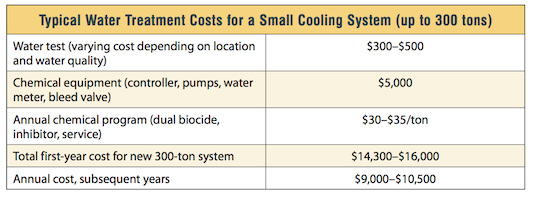
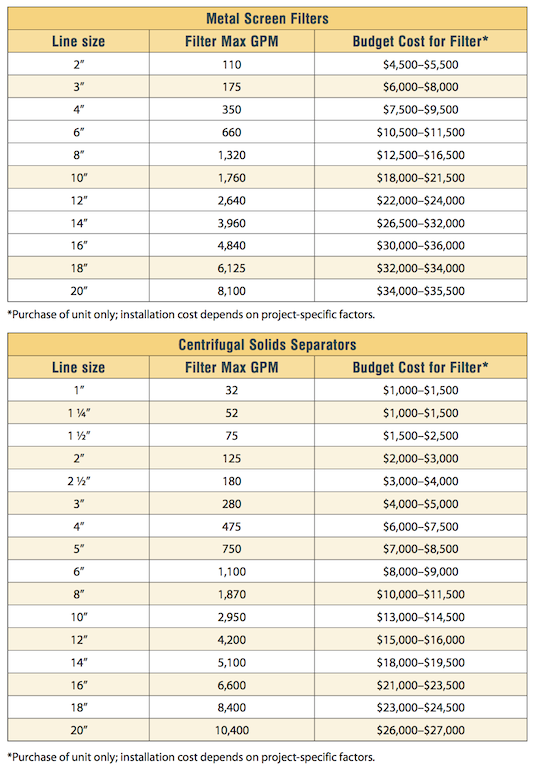